Health and safety in the workplace
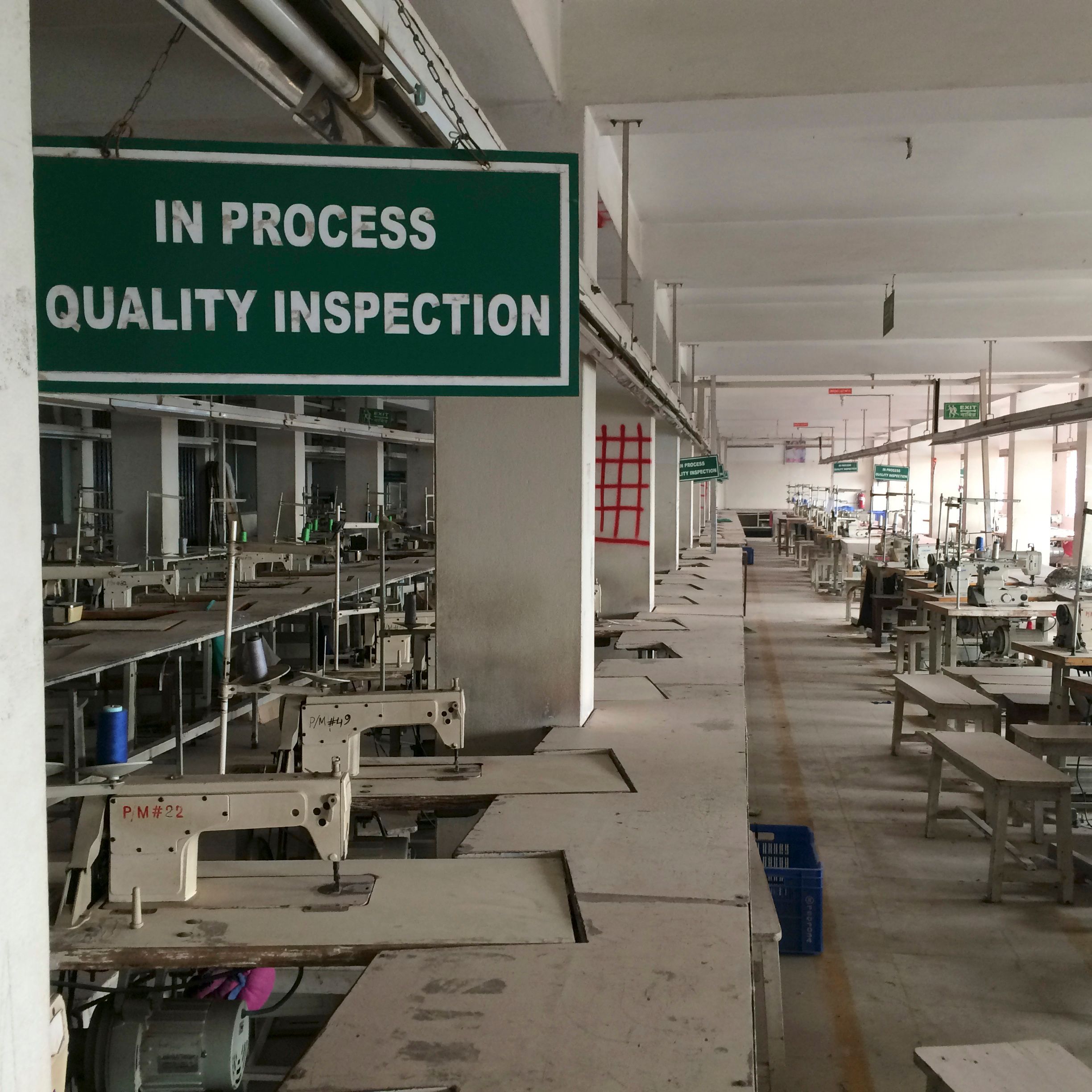
Many textile factories are in a shocking state. There is a risk of entire buildings collapsing because important repairs have not been carried out, or because they are overloaded with additional floors constructed at a later date, or machinery that is too heavy. The most basic safety measures, such as fire exits, fireproof doors, or reliable electrical installations are often missing. There are fire risks in many different areas, as goods are often not stored in an appropriate way.
And the thousands of men and women who are working in backyard workshops are even more vulnerable than their colleagues working in the factories. These sweatshops often do not comply with any regulations, and are never inspected. The workers often work without any protective clothing and in unsuitable premises.
Structural safety of buildings
The collapse of the Rana Plaza is to date the single biggest catastrophe that has occurred in the history of the garment industry. On 24th April 2013, the building collapsed.
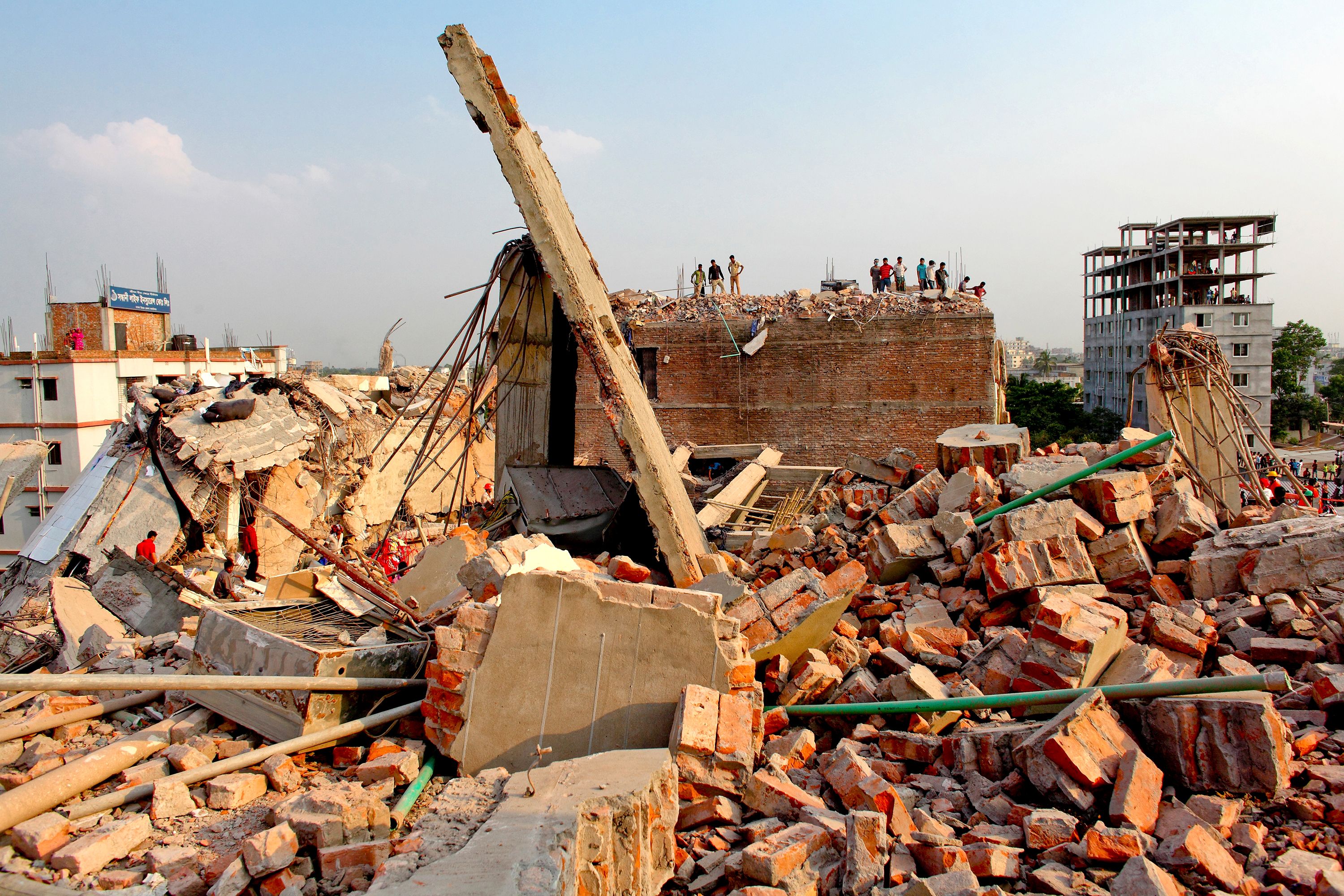
It was nine floors high, and housed five different textile workshops in Savar, near Dhaka, the capital of Bangladesh. A total of 1138 people lost their lives, and over 2000 others were injured. The audits performed by the Business Social Compliance Initiative (BSCI) in two of the five factories just a few months before the collapse had not noted any serious safety defects. As early as 2005, the Clean Clothes Campaign (CCC), coordinated in Switzerland by Public Eye, had requested a sustainable solution to resolve issues linked to the safety of industrial buildings, following the collapse of the “Spectrum” factory in Bangladesh. This tragedy had cost the lives of 64 people. Joining forces with local unions, CCC took the first steps towards an agreement on the structural safety conditions of buildings in Bangladesh.
Fire protection and safety of electrical installations
As well as the safety measures linked to the structural aspects of buildings, fire protection is one of the key areas for guaranteeing safety in the workplace. When fires break out, the lack of safe fire exits, locked doors, barred windows or defective fire extinguishers are the cause of much loss of life. An example of this was in February 2010 at the Garib & Garib factory in Gazipur in Bangladesh, where fire broke out and 21 people lost their lives, with 50 others injured. The fire broke out on the first floor, and was the result of an electrical short circuit. It spread extremely rapidly to the upper floors, where highly flammable fabrics had been stored. Furthermore, the fire exits were blocked, and those working on the top floor were imprisoned by the flames.
-
© GMB Akash / Panos
-
© Andrew Biraj / Reuters
-
© Christa Schröder / Südwind
The workers in the Pakistani company Ali Enterprise suffered a similar fate on 11th September 2012 in Karachi. This fire was the worst tragedy to have ever occurred in the Pakistani garment industry: 254 people perished in the flames that destroyed the building. The safety exits were blocked, the windows barred, and the stairwells inaccessible, which made it impossible for half the factory staff to escape the building once it had caught fire. This drama is all the more shocking, as the company had been audited just a few weeks before the fire, and had been granted the SA8000 international safety certification, which is supposed to guarantee the respect of labour law norms and safety conditions in workshops. After a four-year wait, the company’s main client, the German firm KiK, finally agreed to sign an agreement to compensate the victims.
Another particularly devastating fire occurred on the 24th November 2012 in the Tazreen factory in Dhaka, the capital of Bangladesh. 112 people perished in this tragedy. The fire-escape doors were locked, and the workers remained locked in the building. In spite of the flames that had engulfed the ground level, the workers were forced to continue with their jobs. When a member of staff realised that there was no safe way out to escape the flames, panic broke out. The exit was blocked, the lights went out, and smoke filled the workshop. It was so bad that the desperate employees started jumping out of the windows.
Health protection
Textile industry workers are often exposed to toxic substances, although they often work with no protective clothing and use techniques that endanger their health. Sandblasting jeans involves one of the greatest health risks of all. Jeans are manually sandblasted to get the stonewashed “used” or vintage look. This treatment comes at a cost: the health and indeed sometimes the life of the sander is at risk, and they may even develop an acute form of silicosis. This lung disease is caused by inhaling dust that contains silica particles. And to date there is no known remedy.
Working leather also presents serious health risks. The chemical products and adhesives that are either already present in the leather, or used to make leather goods, can cause respiratory diseases and skin infections, burns and damage to organs. Tanneries work in several stages that use chrome, which is a carcinogenic substance. Workers who then make goods using leather, such as shoes, are often exposed to this toxic chemical product.