Unboxing Shein Shein – the ghost of Liège
Timo Kollbrunner, 12. November 2021
In early January 2021, a small celebration was held at the airport of Liège. The Wallonian government was presenting a certificate of honour to a Chinese businessman called Liansen Tan. His accomplishment was that, six years ago, he provided Liège airport and thus the region of Wallonia with access to the Chinese market.
Chinese companies’ activities have been a topic of heated debate in the region since late 2018. At the time, the e-commerce giant Alibaba announced that it intended to build a huge logistics centre at the airport. Some people in Liège – a former steel powerhouse – associate the arrival of China’s counterpart to Amazon with the prospect of 900 urgently needed jobs. Others vehemently oppose the expansion plans at the airport under the banner of “Stop Alibaba & Co”. They fear clouds of jet fuel exhaust, a procession of lorries, and night flights every few minutes.
And this all began with Liansen Tan. Last year, on the blog “expattime.be” he explained how he had landed in Belgium on a rainy morning in November 2014 with the task of setting up a logistics centre for the online shop of an old schoolfriend: Xu Yangtian, the founder of Shein. Liansen Tan called the company in Liège the “EC Hub”, short for e-commerce hub. Liansen Tan states that they had been pioneers in building a returns processing centre for the whole of Europe. One that could also take on the task of sending out packages again, so that the products “no longer had to be sent back to China”, he explains, not without pride.
Unsuccessful spontaneous application
If you look up EC Hub online, you quickly encounter reviews from ex-employees on the employer review website Glassdoor, the employment website Indeed or on Google. The image that one forms from around 80 reviews is not pretty. There is a wide range of complaints. The most commonly criticized aspect is the “abnormal quotas” that are “impossible to reach”. Yet if you don’t meet the prescribed number of items to be processed, you risk losing your job. Many complain about “Chinese standards” and one statement that sums up the situation reads:
“I’d advise against it. Unless you want to fall into a depression. This company is anything other than humane.”
I don’t want to become depressed, but the reviews do make me curious. I apply to an – already outdated – Facebook job advert in which EC Hub is seeking 30 temporary workers. The answer comes back the next day: there is no need currently, but “we will get back in contact with you if we are looking for workers again”.
We don’t want to wait that long. Fortunately, we are put in touch with Cédric Leterme by our Belgian colleagues from achACT. Cédric is a political scientist with Gresea who is researching, among other things, e-commerce. He is also active in the movement opposing Alibaba’s plans at Liège airport. He has not heard of EC Hub or Shein when we speak to him for the first time. However, he has the most important asset in a situation like this: the right contacts.
Sudoku, crisps and nothing to do
On a Tuesday morning in September 2021, Cédric and I sit around a desk in the centre of Liège with four other people: Daniel Maratta, provincial secretary of the UBT-FGTB union, his colleague Ludovic Moussebois from the other large union CSC-Transcom, as well as Robert and Simone, who both work at EC Hub (we have given them false names). However, they point out that the word “work” is no longer really appropriate. They no longer actually “work” there, because since late July they have no work to do. They show us a video on a mobile phone – a handful of workers sitting around a table in a large, empty warehouse hall, who laugh and wave. Between them there are Haribo sweets, crisps, a Sudoku book and a game of UNO. “We’ve got really good at these games”, says Robert.
Such a scenario was hard to imagine in late June. On just one day in that month, over 30,000 returns were being packaged, recorded and stored at EC Hub, while at the same time approximately 23,000 items were being packaged for despatch, as can be seen from one of the messages sent at the end of a working day from one team manager to another. “Things were crazily busy back then”, says Simone, seeming rather surprised herself.
Shift work and Google Translate
Simone works with returns. Her task is to open packages that arrive from Belgium, Germany, Italy or Switzerland, unpack the items of clothing, scan them into the system and initiate the refund. Purchase costs are reimbursed regardless of the state of the piece of clothing, she explains. This is for two reasons: firstly, because Shein clothes quite often have faults when they leave the factory; and secondly, because the IT system is not sophisticated enough to process non-returnable items separately. “This system is one of the most tedious things about my job”, laments Simone. The main reason for this is that the user interface is in Chinese. “We usually try to figure out what we need to do by using Google Translate.”
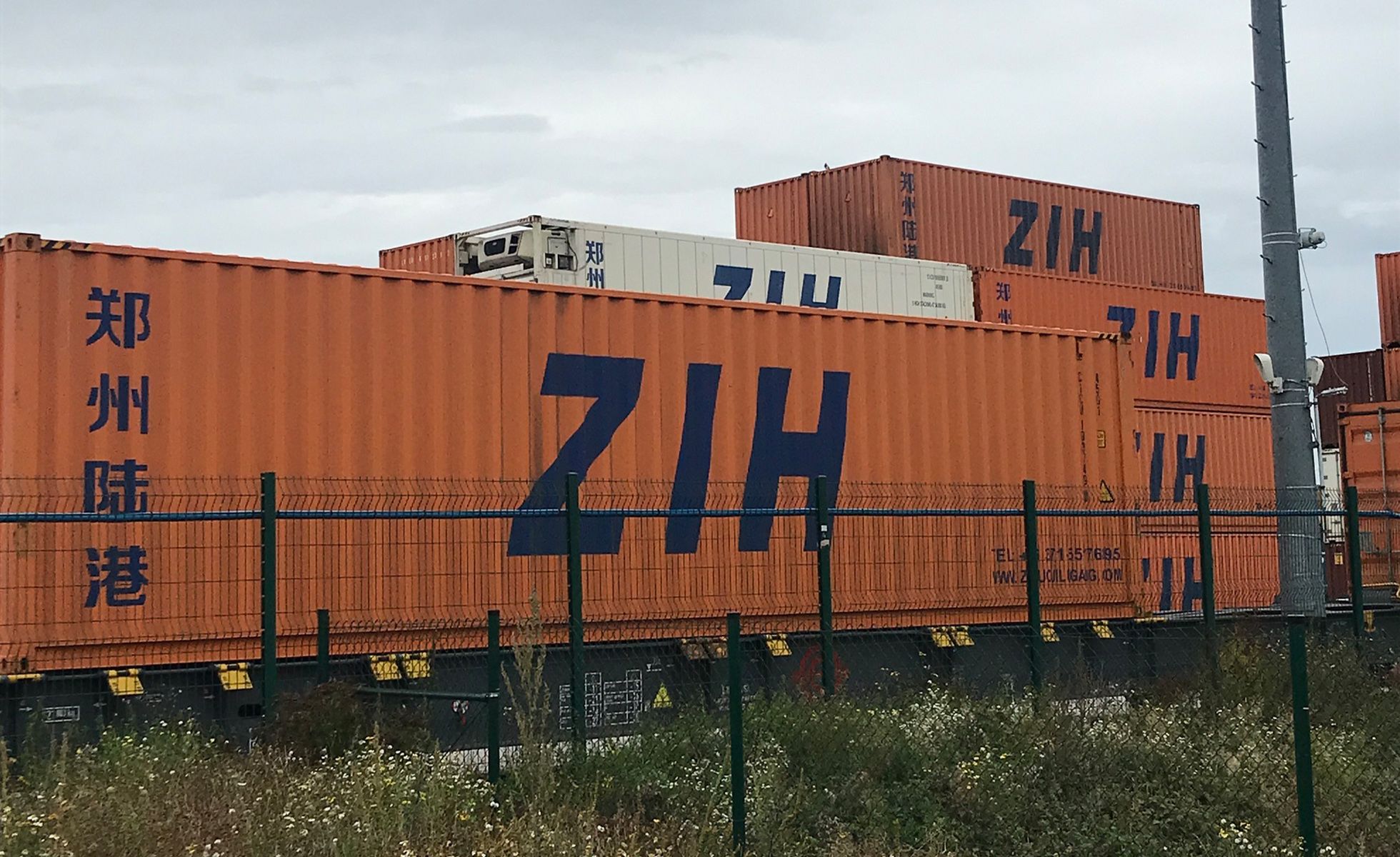
1,500 useless items per day
Simone has worked at EC Hub for many years now, and has experienced Shein’s rapid rise to success in real time. She explains that at the beginning they didn’t stock the returned items. However, the number of returns they received then rose exponentially, and with it the number of items of clothing that were either faulty or that they simply couldn’t find in their internal system, and therefore couldn’t store in the right place. Simone relates that in recent times this had been the case for 20 to 30 articles per shift.
Multiply that by 25 employees, and then by two shifts a day, and that makes up to 1,500 articles a day that Shein no longer had any use for.
To begin with, employees could take these clothes home. Later on, faulty returns were assigned to charities, and finally they were sold per kilo to a trader who removed the Shein labels and sold the clothes “somewhere outside Europe”.
Robert’s job was to arrange returned clothing in broad categories in the warehouse – T-shirts in one place, jackets in another, and jeans elsewhere. His task would hardly have been taxing, except for the performance targets. When he started working for Shein in the Summer of the previous year, the target was to store 1,600 articles per day. That was just about manageable, unless the boxes in the warehouse were already so full that you lost too much time looking for one with enough space to store new items. Then the targets were raised to 1,800 articles – “and that happened in winter when there were many more thick, heavy clothes and when it’s difficult to find space anyway”, states Robert. Failure to meet targets was by far the most frequent cause for dismissal, the two reported. Temporary employees often left after just one day.
Trade unionists bite on granite
Neither Daniel nor Ludovic’s trade unions managed to hold EC Hub to account. Ludovic explains that the closest they got was in Spring 2020, after they received numerous calls from employees. They had complained about sudden changes to working hours, unjustified dismissals, the lack of parking places and about the wages. Nearly all employees had been employed as “Magasiner type 1” – the lowest category of wage, i.e. EUR 12.63 gross per hour. Daniel’s trade union champions a sector-wide minimum wage of EUR 14 per hour. More importantly, he insists that the lowest category of income should only be applied to employees who undertake single, repetitive tasks, adding: “At EC Hub, that’s clearly not the case”. He and Ludovic sought to explain this and other issues to the Chinese management. The woman listened and nodded, “but she probably only understood what she wanted to understand”, says Ludovic.
Setting up a trade union delegation within EC Hub also proved to be an impossible exercise, because doing so would require a quarter of the workforce to sign a declaration stating that they want to unionise. Given that most employees were only employed for a few weeks, it was an impossible task. “We gave it up” laments Daniel.
A sudden turnaround
According to the data in a Belgian corporate directory, the majority of EC Hub workers are employed on permanent contracts. However, looking at consistent statements from the two employees and the trade unionist, that’s simply not correct. This was exactly the topic raised at the beginning of the year, when they had contact with the company’s management for the last time, says Daniel.
Management had contacted them to sign an agreement so that in future it would be possible for employees to work at the warehouse at the weekend. The trade unionists were prepared to negotiate – but only on the condition that EC Hub provided significantly more employees with permanent contracts, namely at least 50 instead of the 25 that had a permanent contract at the time. The company did then employ a few more workers on permanent contracts, but shortly after that there must have been a strategic turnaround. One day in Summer, Simone and her colleagues were suddenly told to no longer carefully package returns, but to stack them, creased as they were, on pallets on which they were then transported out of the warehouse “directly to China”, assumes Simone. Nothing was stored in the warehouse after that. Robert also helped unpack returns, until no more arrived.
It appears that the local subsidiary of the Chinese logistics company YunExpress now handles Shein returns from Europe – or at least a significant part of them. As evidence of this, Simone explains that she had been contacted by a YunExpress employee who wanted to know how the IT system works.
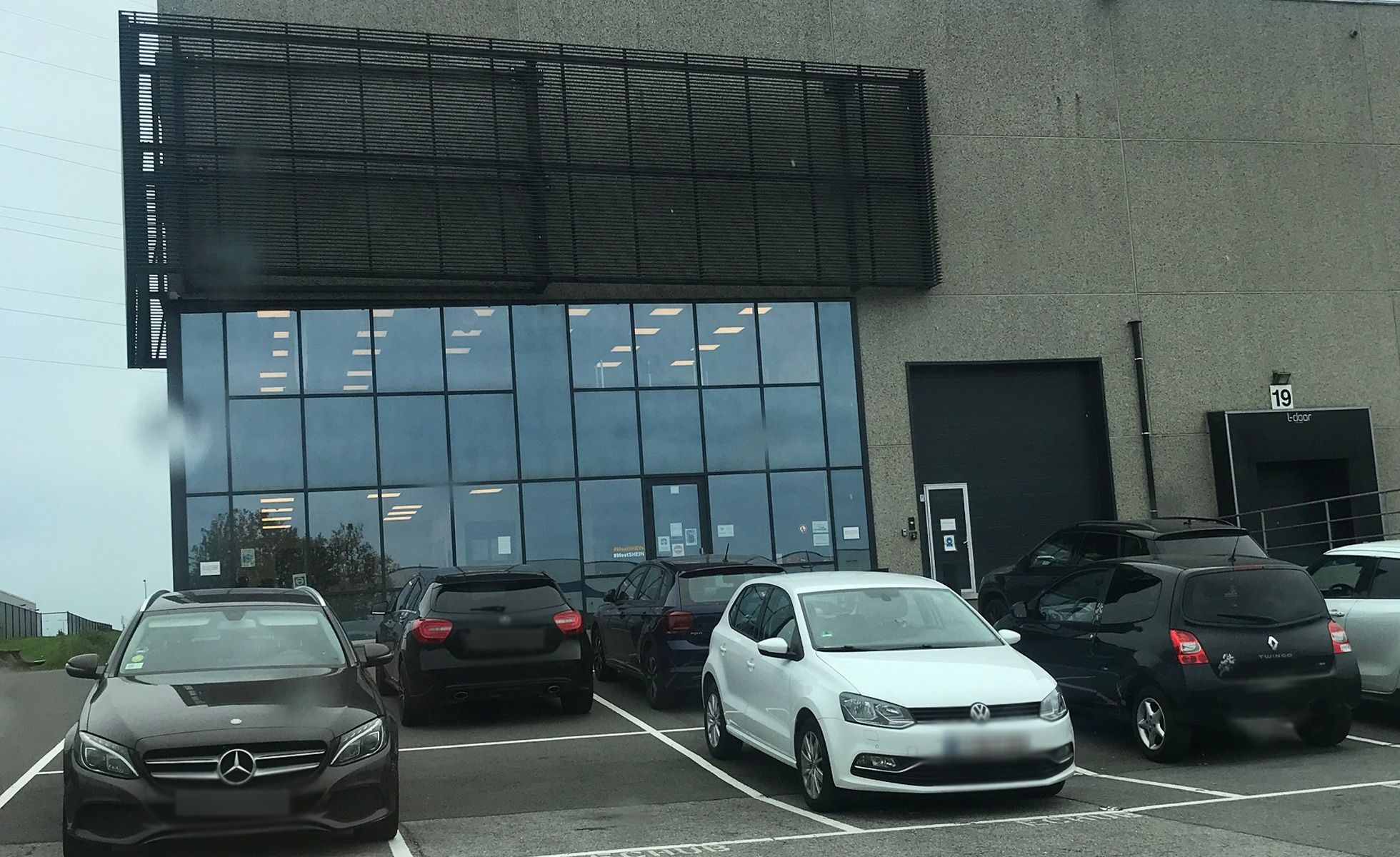
The inspection
We drive out to the industrial area of Herstal and park our car in front of EC Hub. #meetSHEIN is emblazoned on the glass facade. Alongside it, the door to the warehouse is open. Two men are sitting at the entrance, drinking coffee from plastic cups. “We’re waiting for something to start happening here again”, one says. When will this be? “No idea.” In the warehouse, a young man drives an empty forklift around the last remaining pallets stacked with cardboard boxes, while behind him a few employees sit around the white table that we saw in the video.
Two Asian women soon come towards us. They want to know what we’re doing here, but they don’t want to answer our questions, telling us to direct them “to China”. Yes, but where in China? “To our customer.” To Shein? One of the women tells us that she isn’t able to give us an address, but if we want to leave her our contact details, she can pass them onto “the customer”. We do that – and never hear back from anyone.
We want to look around the airport too. In the back corner of the huge logistics complex at the airport of Liège, right next to the train tracks that go all the way to China, YunExpress is located in a recently constructed hangar. Two forklift operators show us the way: “Shein is over there” they say. In a large hangar, where pallets are organized in rows, we meet an employee. He is not particularly chatty either. All he says is that “it’s possible” that the activities of EC Hub were taken over a few weeks ago. He couldn’t say more – we would have to ask Shein directly. Yet he does then say something else: YunExpress is only responsible for haulage; the goods are packed elsewhere. Then he tells us that he has to get back to work.
An uncertain outlook
Robert’s contract with EC Hub runs out soon. After that, he will complete a forklifting qualification and would then like to start working for Alibaba at the airport. Simone will have to wait and see what happens. Until now, management has continually denied that EC Hub would close, she maintains, and adds that finding a permanent job elsewhere would be anything but easy.
Daniel had told us that, recently, YunExpress also contacted the union in order to agree a settlement on weekend working. He had prepared a proposal and sent it to the company. He has not heard anything back so far.